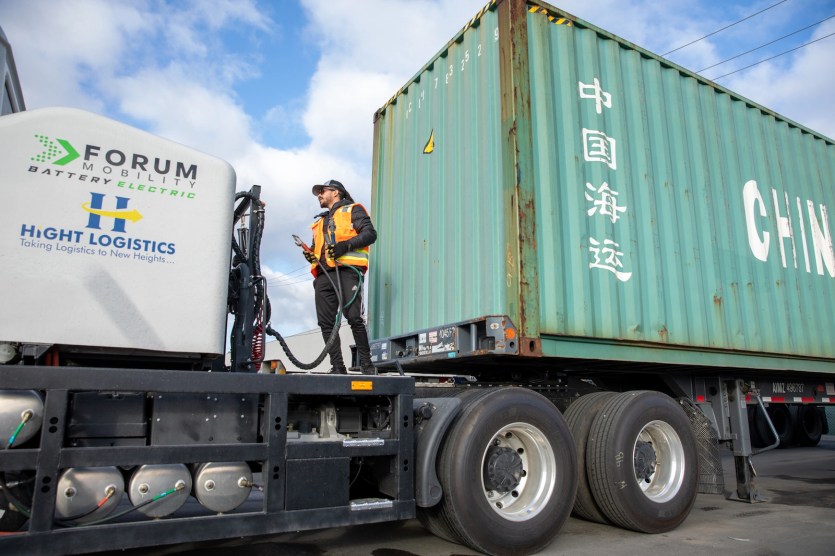
Gabriela Aoun Angueira/Grist
This story was originally published by Grist and is reproduced here as part of the Climate Desk collaboration.
Before the sun rose on a cold January morning, Alex López navigated an 18-wheeler through busy traffic on the 710 freeway. He was headed to the Port of Long Beach, just south of Los Angeles, to retrieve a shipping container and haul it to a warehouse. In the eight years he’s been driving trucks, it was a process López had done thousands of times. “There’s usually nothing new with the routine we have as truckers,” he said.
But on this day, there was something new: He was driving an electric truck.
López drives for Hight Logistics, a family-owned company that moves cargo in and out of the ports of Long Beach and Los Angeles. In January, Hight added four battery-electric trucks to its 50-vehicle fleet. They will mostly haul containers between Hight’s warehouse and the port, a route that cuts through a cluster of communities that have some of the dirtiest air and highest rates of asthma in the country.
Trucks play a foundational role in the US economy. Forty million of them roam the nation, carrying nearly three quarters of its freight. They generate 23 percent of the country’s vehicular greenhouse gas emissions and 32 percent of its nitrogen oxides, or NOx, a main contributor to air pollution. Going electric would significantly cut those emissions and nearly eliminate the NOx.
As the country begins to decarbonize its trucking fleet, drayage trucks—which transport cargo containers from ports and rail yards to distribution centers—provide a logical place to start. They run short routes that require less battery range, and operate out of centralized locations where they could charge. Electrifying them would have a transformational impact on the frontline communities near drayage hubs that struggle to breathe heavily polluted air.
No state has moved more aggressively to decarbonize drayage than California, where 33,500 trucks trundle in and out of ports and railyards. Statewide, medium- and heavy-duty vehicles account for one-fifth of greenhouse gas emissions.
Hight is one of about a dozen fleets in California that have added electric trucks, a number that will grow as companies rush to comply with looming zero-emissions mandates. But as the state’s effort to electrify the sector begins, some fear it is moving too quickly and could drive small operators out of business.
While the Biden administration hopes to see zero-emission trucks make up 30 percent of big rig sales by 2030, California has more ambitious plans. It wants to make all trucks used for drayage zero-emissions within 12 years, and medium and heavy-duty vehicles of all kinds zero-emission “where feasible” by 2045. Massachusetts, New York, New Jersey, and Oregon also are moving to decarbonize drayage.
“It was a wake up call,” Rudy Díaz, Hight’s CEO, said of California’s drayage goal. He knew some of the trucks Hight used would need to be retired, and moved quickly to find zero-emission replacements. “I don’t want to be in a position where the mandates are on top of me and it’s too late.”
No regulation will put more pressure on companies like Hight than California’s Advanced Clean Fleets Rule. It would require that, beginning next year, all newly registered drayage trucks be zero emission. It also mandates that, beginning in 2025, any rigs with an engine 13 years or older be replaced with a zero-emissions truck once it hits 800,000 miles. The California Air Resources Board is expected to approve the rule in April.
The accelerated decarbonization timeline for drayage is an acknowledgement of the logistical challenges of electrifying long-haul trucks. About half a dozen manufacturers offer battery-electric big rigs, but none offer more than about 200 miles of range. Charging can take hours, an impractical proposition for a driver who must cover 500 miles in a day.
“If you’d told me five years ago that batteries were going to haul freight, I’d have said no way,” said Mike Roeth of the North American Council for Freight Efficiency. “Now, manufacturers have started to deliver, but it’s still very early stages.”
Early, but perhaps far enough along for drayage. The trucks often travel just 50 to 100 miles daily and could charge between shifts. “Because they have a contained route, it’s a predictable, controlled atmosphere,” said Roeth.
Focusing on transportation around ports and rail yards also addresses the industry’s toxic impact on frontline communities. According to Roeth, drayage has historically been the realm of older, less reliable vehicles. “Drayage is where diesel trucks used to go to die,” he said. “They were spewing emissions.”
Those pollutants expose residents to dangerous levels of ozone and particulate matter that can cause respiratory conditions, cardiovascular disease, and other illnesses. This is true of the cities around the ports of Long Beach and Los Angeles, which sit alongside each other on San Pedro Bay. Together they comprise the largest port complex in the United States and the ninth largest in the world. “There’s 6,000 trucks that go in and out of the port every day,” said Long Beach Mayor Rex Richardson. “The most significant driver of poor air quality is diesel exhaust from those trucks.”
Richardson said Long Beach residents closest to the ports and freeways have a life expectancy 14 years shorter than those who live further away. Many neighborhoods in the nearby communities of Carson, Wilmington, and West Long Beach rank in the 99th percentile in the state for emergency room visits related to asthma.
“The communities have been treated like pass-through dumping grounds for industry to continue to operate in a way that is really out of date,” said Sylvia Betancourt of the Long Beach Alliance for Children with Asthma. The alliance helps families manage childhood asthma, but Betancourt said all those trucks make that difficult. “When children are constantly exposed, no amount of medicine will help,” she said. “How do you expect a child [to manage] when you have trucks that are idling just outside their playground?”
Truck pollution isn’t the only culprit. The area is also home to oil refineries, railyards, chemical facilities, and an oilfield. Although particulate pollution around the ports has dropped significantly in the last two decades due to more stringent pollution standards, Betancourt said that’s not the experience of people who live alongside industrial sites. Mario Díaz Salazar has lived in a small house on Pacific Coast Highway, one of the area’s busiest thoroughfares, in West Long Beach since 2010. Trucks queue up to refuel at the Chevron station next to his home, which is constantly exposed to pollution.
“I actually have a cup of soot that I’ve collected,” he said. “It looks like dirt, but it’s not dirt. It’s a combination of exhaust emissions and maybe brake dust.”
If California’s Advanced Clean Fleets rule goes into effect as expected, some fleet operators would have to buy zero-emissions vehicles as soon as next year. Advocates for trucking fleets said that would be impossible for many operators.
“The road to get there will be littered with the corpses of businesses that no longer are going to be able to afford to do business in California,” said Matt Schrap, CEO of the Harbor Trucking Association, a trade organization that represents drayage fleets on the west coast.
An Air Resources Board spokesperson said in an emailed statement that the board is still taking public comment on the regulation. “We listen to trucking industry concerns as well as those of other parties, including utilities, environmentally impacted communities, and environmental advocates.”
The Inflation Reduction Act, signed into law last year, includes a tax credit of up to $40,000 for battery-electric trucks and 30 percent of the cost of a charger. California offers a $120,000 rebate for battery-electric big rigs and, in some cases, as much as $410,000 to scrap an old polluter for a zero-emissions machine. But for some operators, the cost of a zero emissions vehicle may still be prohibitive. A battery-powered truck can cost as much as half a million dollars with taxes and fees. That’s more than twice what a diesel costs.
Before joining Hight full-time to drive one of its electrics, López drove under a contract for the company while operating two diesel rigs of his own. He said independent drivers are already under financial strain and buying a new zero-emission vehicle won’t be feasible for many of them. “These people had their trucks paid off,” he said. “They don’t want to finance again and fall into another debt.”
Schrap said getting loans can be difficult, and some banks are reticent to finance them because there isn’t an established resale market for vehicles that might be repossessed. The financial impacts go beyond the hefty up-front cost. Because of their enormous batteries, the vehicles can weigh around 10,000 pounds more than their diesel counterparts. Federal law limits a loaded truck to 80,000 pounds (the law grants electrics an additional 2,000 pounds), forcing drivers to haul less cargo. That means less profit.
Drivers may also need to reduce the number of trips they make in a day. The electric semi López drives provides a real-world range of about 130 miles—fine for going from the port to Hight’s warehouse, but not enough to reach Southern California’s inland valleys. “How long it lasts is the limitation,” he said. “How do you tell a customer that you can’t take your truck to them because you don’t have the range?”
Charging in the middle of a shift would take too long, and assumes drivers can find charging stations. The Port of Long Beach currently has just two. “Infrastructure is what keeps us up at night,” said Schrap. “This is where environmental justice groups and the trucking industry should be on the same page to say to the state, ‘Show us that there’s going to be enough energy deployed to support these trucks.’”
The California Energy Commission estimates that supporting the 180,000 medium- and heavy-duty trucks it hopes to see on the road by 2030 will require installing 157,000 chargers. That’s 52 per day, every day, for seven years. “We need a Manhattan Project for chargers,” commissioner Patty Monahan said at a ribbon cutting ceremony for Hight’s electric fleet.
Hight Logistics installed three charging stations with two ports each to power its four zero-emission trucks. By the end of the year, it plans to have five stations and 10 electric trucks, thanks to its partnership with Forum Mobility, a Bay Area company that wants to make it easier for fleets to decarbonize. Hight pays Forum a monthly fee to use its trucks and charging stations, a model called truck-as-a-service.
“It’s really good to clean up ports, but we can’t crush small businesses at the same time,” said Matt LeDucq, the company’s CEO. Rather than expect fleets to navigate the transition on their own, LeDucq said the key will be building large-scale infrastructure. Forum wants to create a network of centralized depots that can house and charge 50 to 150 trucks from multiple fleets. Operators can use Forum’s vehicles, or drive their own.
By 2024, Forum hopes to offer 500 chargers across California. The company just announced a $400 million joint venture which would allow it to install thousands more over time.
Until networks like these exist, Hight can’t use zero-emissions vehicles on all of its routes. In the meantime, the company is learning how to integrate the new machines. It operates them only during the day, and makes about three runs to the port before plugging in overnight.
“We’re exploring it at the same time as we’re doing it,” said López. On that chilly morning in January, he was making a pickup at the Long Beach Container Terminal, a newly completed, fully electric site. An automated crane hoisted a 40-foot container and placed it perfectly onto the truck’s chassis. “We have to adapt,” he said. “The future is already here.”